Quick and Reliable Packaging Equipment Fixing Services to Lessen Downtime
In the competitive landscape of manufacturing, the effectiveness of product packaging operations hinges on the integrity of equipment. Quick and trustworthy repair services are important in alleviating downtime, which can lead to substantial functional problems and monetary losses.
Importance of Timely Repairs
Timely repair work of packaging makers are vital for keeping functional effectiveness and lessening downtime. In the hectic atmosphere of production and packaging, also small malfunctions can result in significant delays and performance losses. Resolving concerns immediately guarantees that devices operate at their optimum capability, thus protecting the flow of procedures.
Additionally, routine and timely maintenance can protect against the rise of minor problems right into major break downs, which frequently sustain greater repair work prices and longer downtimes. A positive approach to equipment repair service not only maintains the stability of the equipment yet additionally improves the overall integrity of the assembly line.
Additionally, prompt repair work add to the durability of product packaging equipment. Machines that are serviced without delay are less most likely to experience excessive wear and tear, enabling businesses to optimize their financial investments. This is particularly vital in markets where high-speed product packaging is vital, as the demand for consistent efficiency is paramount.
Benefits of Reliable Solution Suppliers
Dependable provider play a critical function in ensuring the smooth operation of product packaging equipments. Their experience not only enhances the effectiveness of repairs however additionally contributes substantially to the long life of tools. Dependable company are equipped with the technical understanding and experience essential to diagnose issues precisely and carry out reliable remedies quickly. This reduces the threat of reoccuring troubles and guarantees that makers run at optimum efficiency degrees.
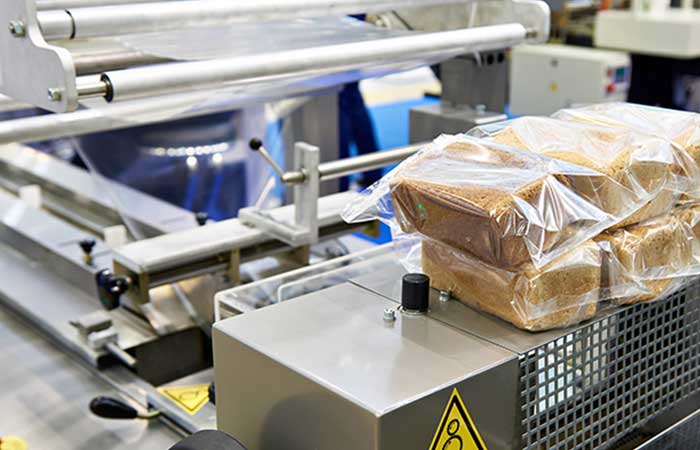
Additionally, a reliable service supplier provides extensive support, including training and guidance for staff on equipment procedure and upkeep finest methods. This not only encourages staff members yet additionally cultivates a culture of safety and performance within the company. Generally, the benefits of involving trusted provider extend past instant repair work, positively influencing the entire operational operations of packaging processes.
Usual Product Packaging Device Concerns
In the world of packaging operations, numerous problems can compromise the performance and performance of machines. One widespread problem is mechanical failing, usually coming from wear and tear or poor maintenance. Elements such as motors, equipments, and belts might stop working, leading to malfunctions that halt production. An additional typical concern is misalignment, which can create jams and uneven product packaging, impacting product top quality and throughput.
Electric problems can likewise interfere with product packaging operations. Defective circuitry or malfunctioning sensing units may result in unpredictable maker actions, causing delays and boosted functional prices. Additionally, software application problems can prevent the machine's programs, causing functional inefficiencies.
Inconsistent product flow is one more important concern. This can arise from variations in product weight, form, or dimension, which may affect the device's capability to manage things accurately. Finally, insufficient training of operators can worsen these issues, as inexperienced workers may not acknowledge early indications of malfunction or might misuse the tools.
Attending to these typical packaging machine issues quickly is important to preserving efficiency and guaranteeing a smooth operation. Normal assessments and positive maintenance can dramatically minimize these worries, fostering a reputable packaging setting.
Tips for Lessening Downtime
To reduce downtime in packaging procedures, executing a proactive upkeep technique is crucial. Regularly set up maintenance checks can recognize prospective issues prior to they escalate, making certain makers operate effectively. Establishing a regimen that includes lubrication, calibration, and examination of vital components can dramatically decrease the regularity of unexpected failures.
Educating staff to operate equipment correctly and identify early indication of breakdown can likewise play an essential role. Encouraging operators with the understanding to execute basic troubleshooting can protect against minor problems from creating major delays. In addition, maintaining an efficient supply of important extra components can expedite repair services, as waiting for parts can cause extended downtime.
Additionally, documenting maker efficiency and upkeep tasks can help identify patterns and frequent troubles, allowing for targeted interventions. Integrating sophisticated surveillance modern technologies can provide real-time data, allowing anticipating maintenance and minimizing the risk of unexpected failures.
Finally, promoting open communication between operators and maintenance teams guarantees that any irregularities are quickly reported and dealt with. By taking these proactive measures, businesses can enhance operational performance and dramatically lower downtime in product packaging procedures.
Selecting the Right Repair Work Service
Selecting the appropriate fixing solution for packaging devices click now is a vital decision that can significantly influence functional efficiency. A well-chosen company guarantees that your machinery is fixed quickly, efficiently, and to the highest criteria. Begin by examining the supplier's experience with your particular sort of product packaging devices. A service technician accustomed to your equipment can identify concerns a lot more precisely and implement remedies a lot more rapidly.
Following, think about the company's online reputation. Seeking responses from other companies within your industry can supply understandings into dependability and top quality. Accreditations and collaborations with identified equipment makers can also indicate a dedication to quality.
Additionally, evaluate their action time and schedule. A company that can supply prompt support lessens downtime and maintains production flow consistent. It's additionally crucial to ask about service warranty and solution warranties, which can reflect the confidence the company has in their job.

Verdict
In verdict, the relevance of fast and dependable product packaging device repair solutions can not be overstated, as they play a critical function in decreasing downtime and making certain operational efficiency. By prioritizing prompt repair services and selecting trustworthy company, businesses can successfully deal with usual issues and preserve efficiency. Implementing positive upkeep practices and investing in team training try this further improves the long life of packaging machinery. Inevitably, a strategic method to fix solutions fosters a much more resistant manufacturing atmosphere.
Prompt fixings of packaging machines are important for preserving operational effectiveness and reducing downtime.Furthermore, timely repair services add to the durability of product packaging machinery. In general, the benefits of engaging dependable solution providers extend beyond immediate repairs, favorably influencing the whole operational operations of product packaging procedures.
